Book Appointment Now
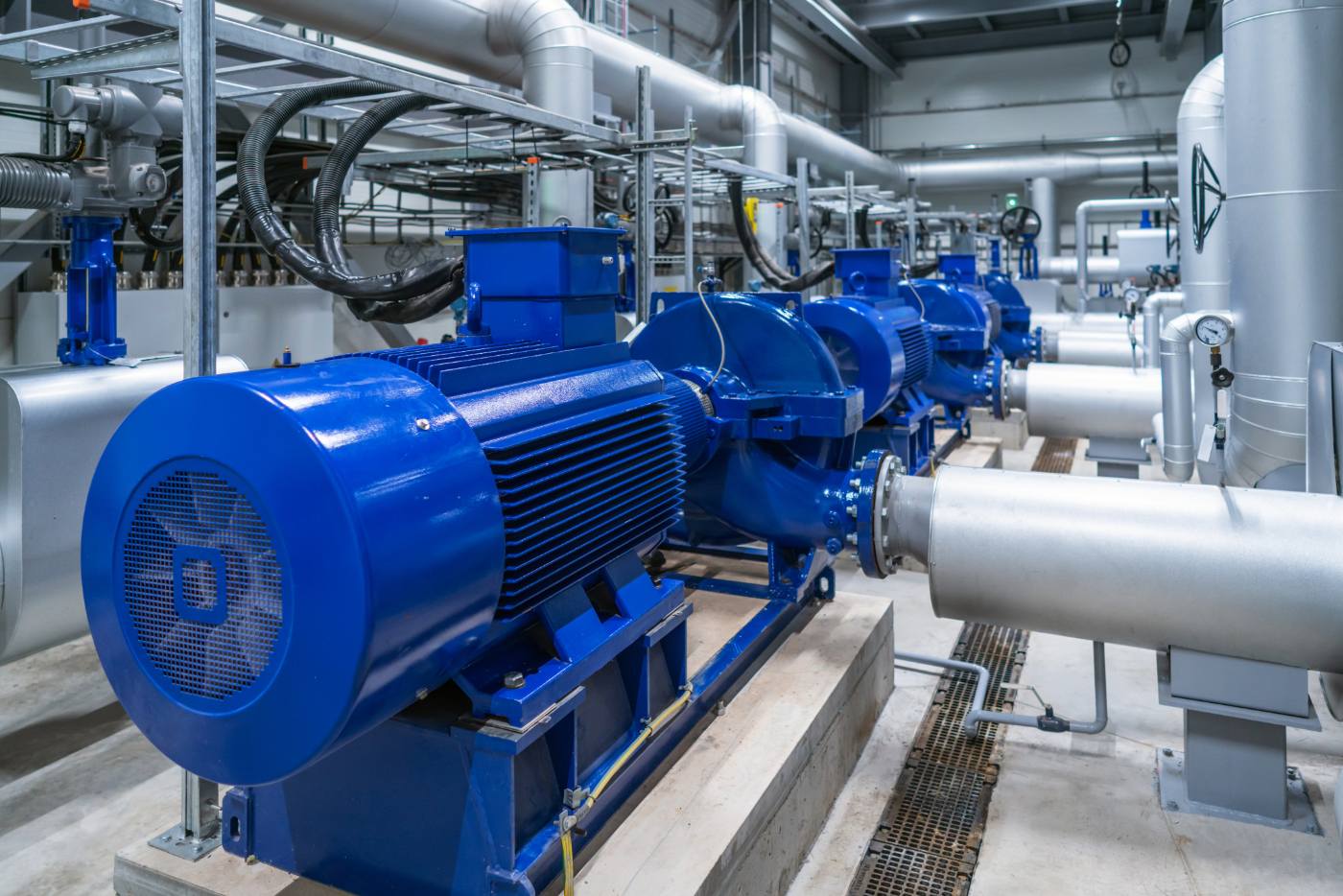
Industrial Pumps Uncovered: The Latest Innovations and Trends You Need to Know
In today’s industrial landscape, industrial pumps are the unsung heroes powering essential processes across countless sectors. From transporting crude oil in the energy sector to handling abrasive slurry in mining operations, and from circulating cooling fluids in manufacturing plants to managing wastewater in treatment facilities—these mechanical systems are central to operational efficiency and reliability. Their performance directly impacts productivity, environmental compliance, and overall equipment longevity.
As industries grow more complex and demand for automation, sustainability, and efficiency continues to rise, the role of industrial pumps has evolved. No longer just a basic utility, modern pumps are becoming smarter, more energy-efficient, and tailored for specialized applications. Significant technological advancements and a surge in demand for more adaptive solutions are driving this transformation.
This article explores the latest innovations in pumping technology, current trends shaping the industry, and emerging technologies that are revolutionizing fluid handling. Whether you’re a facility manager, engineer, or procurement specialist, staying informed on these developments is essential. Additionally, we’ll highlight how leading industrial pump companies are setting new standards in product development, maintenance services, and sustainability. Choosing the right pump isn’t just about performance—it’s about future-proofing your operations in an increasingly competitive environment.
A Quick Recap: What Are Industrial Pumps?
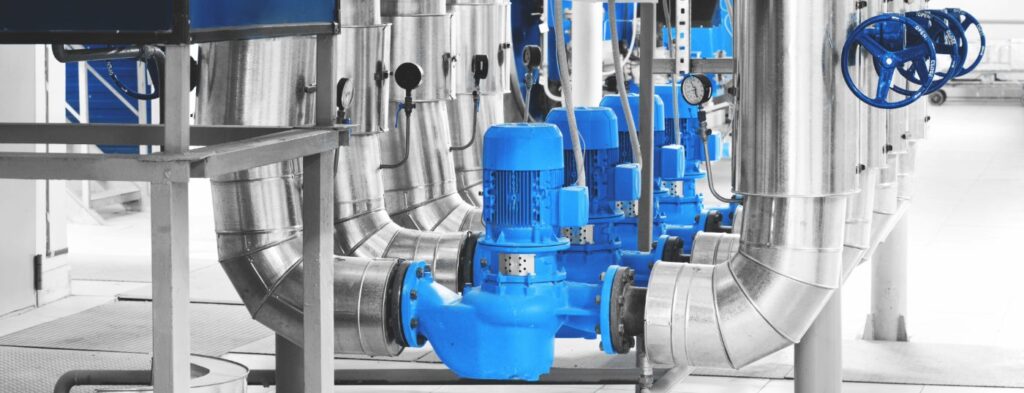
Industrial pumps are mechanical devices designed to move fluids—such as water, chemicals, slurry, or oil—from one location to another, typically within large-scale or high-demand environments. They are critical to maintaining continuous operations in industries like oil and gas, mining, manufacturing, agriculture, pharmaceuticals, and water treatment. Depending on the application, these pumps are selected based on the type of fluid, required pressure, flow rate, and environmental conditions.
There are several key classifications of industrial pumps, each suited for specific uses. Centrifugal pumps are the most widely used type and operate using rotational energy from a motor to move fluid through a system. They are ideal for low-viscosity liquids and high-flow applications. Positive displacement pumps, which include gear, diaphragm, and piston pumps, are better suited for high-viscosity fluids and provide consistent flow regardless of system pressure. Submersible pumps are designed to operate while fully submerged in fluid and are commonly used in dewatering and wastewater management. Specialty pumps, such as magnetic drive or peristaltic pumps, are tailored for corrosive, hazardous, or sensitive materials.
Industrial pumps serve a range of critical functions across industries—transferring chemicals in processing plants, feeding boiler systems in power generation, removing groundwater in construction, and managing sludge in wastewater facilities, to name a few.
To meet the diverse demands of these industries, industrial pump companies are continuously innovating and customizing pump designs. These companies not only manufacture pumps but also provide system engineering, integration, and lifecycle support tailored to each application. They factor in variables like fluid characteristics, environmental conditions, energy consumption, and long-term maintenance to deliver optimal pumping solutions.
With efficiency, reliability, and adaptability at the core of system design, industrial pump companies play a pivotal role in helping industries streamline operations and minimize downtime. Understanding the fundamentals of industrial pumps and their various types is essential when evaluating equipment for your specific operational needs.
Cutting-Edge Innovations in Industrial Pumps
The rapid evolution of technology is transforming how industries approach fluid handling, and industrial pumps are at the forefront of this innovation. Today’s systems are more intelligent, efficient, and resilient than ever before—thanks to significant advances in design, manufacturing, and digital integration.
One of the most transformative developments is smart pump technology. Leveraging the Internet of Things (IoT), smart industrial pumps are equipped with sensors and connectivity features that enable real-time diagnostics, performance monitoring, and predictive maintenance. This allows operators to detect anomalies before failures occur, reducing downtime and extending equipment life. Such capabilities are increasingly essential for facilities seeking to minimize unplanned maintenance and optimize operational efficiency.
Energy efficiency has also become a top priority for industrial pump companies. Modern industrial pumps now incorporate variable frequency drives (VFDs), which adjust motor speed based on flow demand. This results in substantial energy savings, especially in systems that experience fluctuating loads. Additionally, magnetic drive pumps eliminate the need for mechanical seals, reducing both energy loss and leakage risks.
Material innovation is another area where progress is reshaping the landscape. Corrosion-resistant alloys and engineered composites are extending the life of pumps used in harsh or corrosive environments. Some manufacturers have even begun using 3D printing for custom components, which accelerates prototyping, reduces waste, and enables greater design flexibility.
Space-saving designs are also gaining traction. Today’s industrial environments often face limitations on floor space and noise control. In response, pump manufacturers are developing quieter, more compact systems that meet facility requirements without compromising performance.
The cumulative benefit of adopting these next-generation technologies is significant. Industrial pumps that incorporate smart monitoring, efficient energy use, and advanced materials not only lower the total cost of ownership but also enhance reliability and performance.
Industrial pump companies that embrace innovation are setting new benchmarks in the industry, offering solutions that go beyond simple fluid transfer to deliver measurable business value. As market demands continue to evolve, partnering with forward-thinking industrial pump companies is essential to staying ahead in today’s competitive landscape.
Sustainability and Environmental Trends
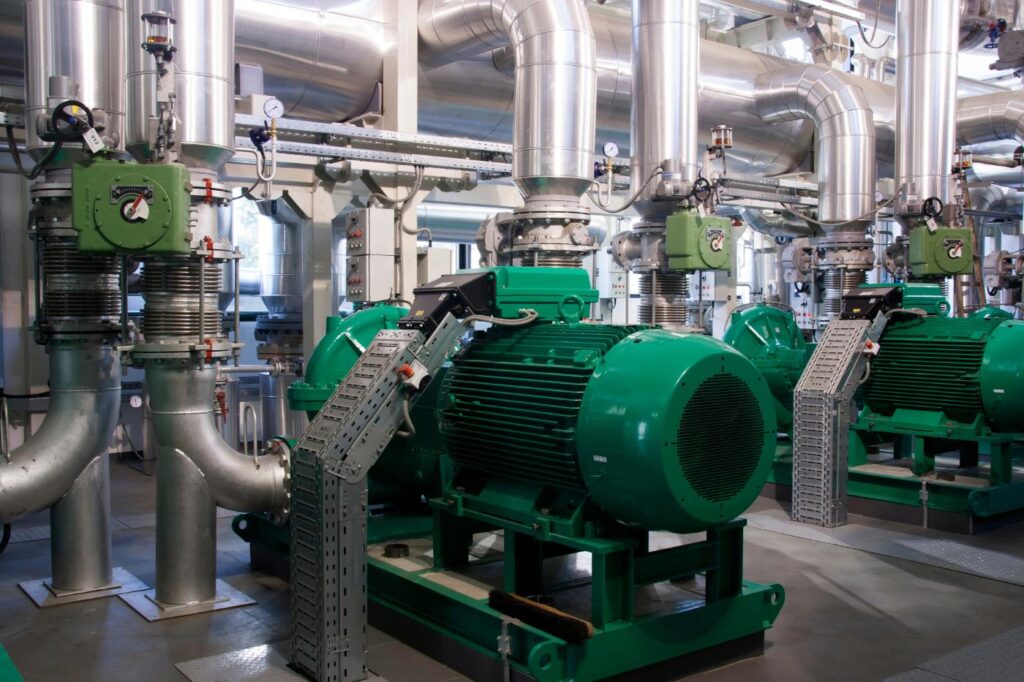
As environmental regulations tighten and sustainability becomes a central focus for industries worldwide, the role of industrial pumps in supporting eco-friendly operations has grown increasingly significant. Across sectors such as water treatment, chemical processing, and manufacturing, there is a strong push toward minimizing environmental impact without compromising performance. In response, industrial pump companies are stepping up with innovative technologies and engineering practices that align with green objectives.
One of the primary ways industrial pump companies are reducing environmental footprints is through the development of energy-efficient systems. Modern industrial pumps are now designed to consume significantly less power, often by incorporating variable frequency drives (VFDs), improved hydraulic designs, and energy-optimized motors. These advancements help lower overall energy consumption, reduce greenhouse gas emissions, and contribute to cost savings over the equipment’s life cycle.
Another important area of innovation lies in fluid containment and leak prevention. Pumps used in chemical and hazardous material processing are increasingly equipped with zero-leakage seals, magnetic drives, and double mechanical seals to eliminate emissions and protect both workers and the environment. This is particularly critical in applications where even minimal leaks could lead to environmental damage or regulatory violations.
Material advancements are also playing a role in sustainability. Industrial pump companies are now using corrosion-resistant, recyclable, and longer-lasting materials that reduce the frequency of pump replacement and the volume of industrial waste. Additionally, modular pump designs allow for easier repairs and part replacements, extending equipment life and reducing material disposal.
Real-world examples of these sustainable practices can be seen in wastewater treatment facilities, where industrial pumps equipped with smart controls adjust flow rates in real time, optimizing energy use and improving system efficiency. In chemical manufacturing, pumps with high containment levels and low energy requirements are helping companies meet environmental compliance targets while maintaining production performance.
In process industries, closed-loop systems utilizing advanced pump technology are minimizing water waste and chemical exposure, further supporting sustainability goals.
As demand grows for cleaner, more efficient industrial operations, industrial pumps are proving to be a key contributor to sustainable development. Forward-thinking industrial pump companies are leading this shift, providing the solutions needed to meet both environmental and operational goals.
Market Shifts and Industry Trends
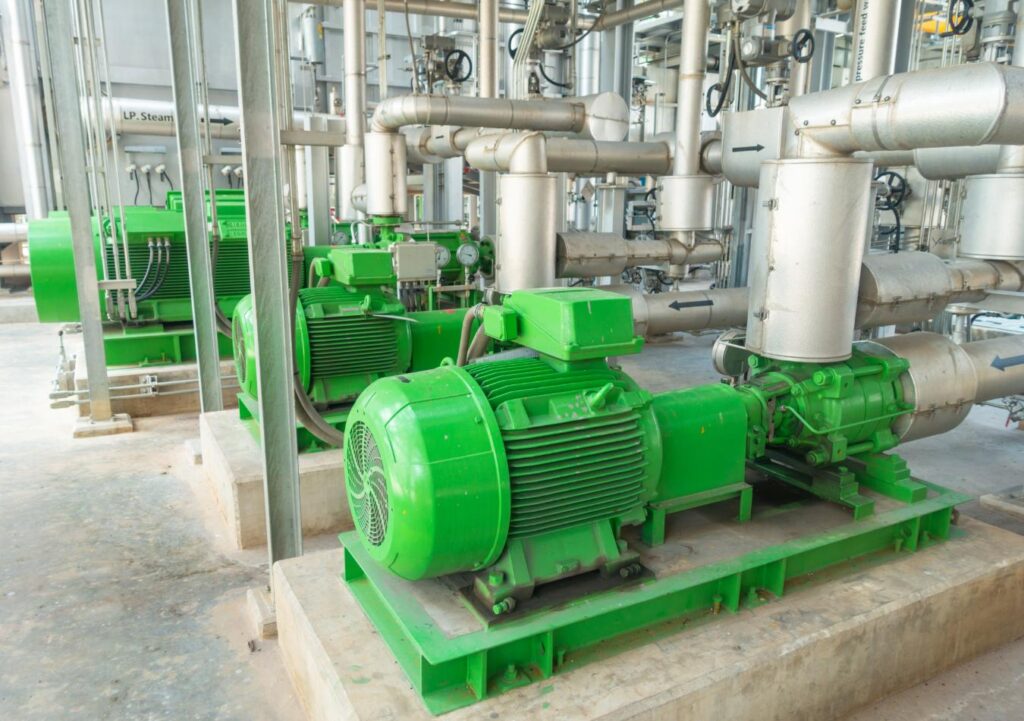
The industrial pump landscape is undergoing a transformation driven by technological advancements, shifting customer needs, and evolving global market dynamics. As industries strive for higher efficiency, lower operational costs, and improved reliability, several key trends are emerging that are reshaping how industrial pumps are designed, deployed, and serviced.
One of the most significant shifts is the growing demand for custom and application-specific pump systems. Rather than relying on one-size-fits-all solutions, industries now seek pumps that are precisely engineered for unique fluid characteristics, pressure requirements, environmental conditions, and installation constraints. This has prompted industrial pump companies to invest heavily in R&D and collaborate closely with clients to deliver tailored solutions. Whether for handling abrasive slurry in mining or managing sensitive chemicals in pharmaceutical production, bespoke pump systems offer enhanced performance and lifecycle value.
Another major trend is the integration of artificial intelligence and automation within pumping systems. Smart factories are leveraging industrial Internet of Things (IIoT) platforms to create interconnected ecosystems where pumps can self-monitor, predict failures, and adjust operating parameters in real time. These AI-enabled industrial pumps reduce downtime, extend service intervals, and optimize energy consumption—transforming them from passive components into intelligent assets that contribute to plant-wide efficiency.
On a global scale, markets in Asia-Pacific and Latin America are seeing robust growth in demand for industrial pumps. Rapid industrialization, infrastructure expansion, and increased investment in sectors like energy, construction, and water treatment are fueling this rise. Industrial pump companies are actively targeting these regions with localized support, competitive pricing, and technology that meets region-specific challenges such as power availability, climate conditions, and regulatory frameworks.
Another important shift is the emergence of service-based business models, particularly maintenance-as-a-service (MaaS). Instead of purchasing pumps and managing maintenance internally, many companies are now subscribing to performance-based services where the pump supplier is responsible for monitoring, maintenance, and uptime guarantees. This not only reduces capital expenditures but also ensures that systems operate at peak efficiency without requiring extensive in-house technical expertise.
These market shifts reflect a broader evolution in how industrial pumps are viewed not just as equipment but also as strategic tools for achieving operational excellence. By adapting to these trends, industrial pump companies are positioning themselves as essential partners in their clients’ growth and sustainability journeys.
Conclusion
The world of industrial pumps is evolving rapidly, driven by innovations in smart technology, energy efficiency, sustainable design, and global market demand. From IoT-enabled diagnostics and AI integration to custom-built systems and eco-conscious materials, the latest advancements are transforming how industries approach fluid handling and system reliability. These developments not only improve operational performance but also offer long-term cost savings and support environmental compliance goals.
Staying informed about these trends is no longer optional—it’s a competitive necessity. As industries become more complex and expectations for uptime, efficiency, and sustainability increase, having the right pumping solutions in place can make a measurable difference in productivity and profitability.
To stay ahead, businesses must go beyond standard equipment and partner with experts who understand the nuances of their specific operations. Leading industrial pump companies offer more than products—they provide engineering support, application insight, and lifecycle services that align with your goals and challenges.
If you’re exploring ways to upgrade your systems or need guidance on selecting the right technology, now is the time to act.
Contact us for more insights on how next-gen pump technology can elevate your operations. Our team is ready to help you find the ideal solution tailored to your needs.